Material
Torsion springs are manufactured from stainless steel spring wire material no. 1.4310 in compliance with EN 10270 part 3 (AISI 302 / BS 301S21). The tolerances for the wire diameters correspond to DIN specification 2076.
Design
Torsion springs are available from stock with either right (clockwise) or left (anti-clockwise) hand coiling. An catalogue number ending with the letter "R" in the tables indicates a right-hand coiled spring, and a number ending with the letter "L" indicates a left-hand coiled spring.

left-hand coiled

right-hand coiled
In principle, the torsion springs should only be loaded in the direction of the coil. The spring bodies are coiled without pitch.
Legs
Standard legs are straight and extend at a tangent from the spring body ("TS1").
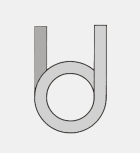
TS 1
We can also supply torsion springs with any forms of legs for an extra charge.
Leg position
Torsion springs are available in stock with leg positions 0 degrees, 90 degrees, 180 degrees, and 270 degrees.
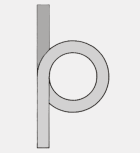
0 degree
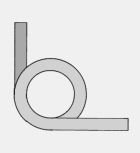
90 degree
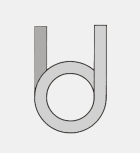
180 degree
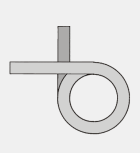
270 degree
Mandrel
Torsion springs are usually operated in conjunction with a mandrel which holds the spring in position. We have provided a range of possible mandrel diameters for each respective torsion spring, as the spring body tends to contract when bending if the mandrel is too large, and to tilt if the mandrel is too small. The smallest possible mandrel diameter in the table is represented by "Ddmin", and the largest by "Ddmax".
Loads
We have stated the maxium possible torque in the column "Mn", as the length of leverage is different in every application. The maximum possible spring load can be determined by dividing "Mn" by leverage "RH":
Fn=Mn/RH
To calculate the load at a particular angle "Alphax" the following formular must be used:
Fx= (Fn/Alphan) x Alphax
Here, Alphan is the largest possible rotation angle given in the table.
Surface treatment
The spiral springs are made from material no.1.4310 and will not be re-coated after production, as surface protection is not normally required. The disadvantage of an additional surface coating for the majority of spiral springs is that protecting the spring bodies in between the coils can only be made at extremely high cost. Here the selection of a suitable material should be made for an additional surface coating.
Production compensation
The spring manufacturers require a production compensation, in order to retain the default parameters. Normally our spiral springs are compensated through the spring's unloaded leg position (Alpha0).
Quality control
Torsion springs are tested for compliance to the tolerated loads and measurements before they are approved and reach the production warehouse. The tests take place in our quality control department according to DIN ISO 2859-1 level II. The procedure normally consists of a simple spot check programme, test-level AQL=1.0. Specific tests can also be carried out and documented for each individual spring upon the customer's request. The following charges apply for the quality control certificates issued by us.
In compilance with:
DIN EN 10204-2.1 (DIN 50049-2.1)
DIN EN 10204-2.2 (DIN 50049-2.2)
DIN EN 10204-2.3 (DIN 50049-2.3)
DIN EN 10204-3.1B (DIN 50049-3.1B)
Testing of prototypes
Calculation
The calculation of torsion springs is carried out according to DIN specification 2088. DIN 2194 Grade 2 is taken as the basic standard for the tolerances.
spring materials
Here you can see a selection of our normal spring materials, they we have on stock. In all questions to the right selection of spring material, please contact our Department Engineering:
Gutekunst Federn · Dep. Engineering · Gewerbegebiet · D-02733 Cunewalde
Tel. (+49) 035877/227-11 · Fax (+49) 035877/227-14 · technik@gutekunst-co.com
surface treatments
Here you can see a selection of our normal surface treatments, they we can produce for you in addition. In all questions to the right surface treatment, please contact our Department Engineering:
Gutekunst Federn · Dep. Engineering · Carl-Zeiss-Strasse 15 · D-72555 Metzingen
Tel. +49 (0)7123 960-193 · Fax +49 (0)7123 960-150 · technik@gutekunst-co.com